Driving Bioprocessing Efficiency Case studies in process intensification and continuous processing
The explosive growth in mAb-based biologics, the globalization of biomanufacturing, and the economic pressures to reduce capital investment, cost of development and cost of goods all point to changes in how biopharmaceutical manufacturing plants are designed, built and operated. Join us as we review the main drivers of change, learn from adopters of transformative technologies, evaluate risk landscapes and collaborate to help set the standards for modern bioprocessing.
Agenda
Registration and Coffee
Welcome and Overview
Towards Flexible Single-use Biomanufacturing: Key Technologies Needed and Lessons Learned
Adam Goldstein, Principal Scientist, Global Manufacturing Sciences, Roche (Genentech)
Economic Impact of Adopting Single-use TFF Flat Sheet Cassettes
Brent Van Rite and Stephanie Wickham, Cytovance Biologics
Abstract
Using Single Use TFF membranes provides increased flexibility for a Contract Manufacturing Organization (CMO) with long term benefits to the processes that use them. Benefits include cost of goods reduction, suite time reduction, and decreased cleaning validation studies leading to a win-win relationship between client and CMO.

Speaker Bio
Stephanie Wickham performed her graduate studies at the University of Oklahoma Health Sciences Center with a Ph.D in Microbiology and Immunology earned in 2009 with a focus on the determination of amino acids responsible for the binding of a bacterial toxin to its mammalian cellular receptor. During her graduate work, Stephanie gained experience in small scale microbial fermentation, transient transfections of mammalian cell lines, small scale affinity purification, UFDF to concentrate membrane vesicles, and conjugation to fluorescent probes. A post-doctoral fellowship was performed at the University of Oklahoma Health Sciences Center in Cell Biology developing small molecule enzyme inhibitors. During her post-doctoral fellowship, Stephanie gained valuable experience with yeast fermentation, enzyme kinetics, UFDF to concentrate fermentation broth, and affinity purification. Following completion of her post-doctoral fellowship in 2012, she joined Cytovance Biologics in the downstream manufacturing group where she gained the experience with large scale purification and its associated equipment, which led to a transition of the Manufacturing Sciences team. Once in manufacturing sciences, Stephanie became versed in mammalian and microbial fermentation in addition to the downstream. She has led this team since late 2014 and facilitated the successful transfer of more than 25 processes to manufacturing that include antibodies, fusion, enzyme, and cytokines.
Economic Impact of Adopting Single-use TFF Flat Sheet Cassettes
Brent Van Rite and Stephanie Wickham, Cytovance Biologics
Abstract
Using Single Use TFF membranes provides increased flexibility for a Contract Manufacturing Organization (CMO) with long term benefits to the processes that use them. Benefits include cost of goods reduction, suite time reduction, and decreased cleaning validation studies leading to a win-win relationship between client and CMO.

Speaker Bio
Brent is currently the Director of Downstream Manufacturing at Cytovance Biologics. He joined Cytovance in 2012 as an on-the-floor production associate and has since advanced into his current role. Brent’s bioproduction experience ranges across a wide array of molecules (MAbs, enzymes, cytokines, fusions, etc.) from mammalian, microbial and transgenic platforms. Brent received his BS in Biomedical Engineering from Michigan Technological University and Ph.D. in Bioengineering from University of Oklahoma in 2012.
Break
XCell™ ATF: 100% Cell Retention with Single-use Implementation Convenience
John Bonham-Carter, Director, Upstream Sales, Repligen
Abstract
Fed batch and perfusion cell culture processes can be intensified with the XCell™ ATF system. High viable cell densities drive improved productivity for many biomolecule types. The availability of XCell™ ATF system in a single-use format drives further efficiencies into product implementation. This seminar will use case studies to demonstrate multiple paths to implementation and assess process impact.
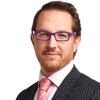
Speaker Bio
John Bonham-Carter is a serial entrepreneur with experience in multiple countries in industries from newspapers to biotechnology. Within bioprocessing, he has worked with many different upstream technologies and, most recently, has propelled the ATF System to become the industry leader in continuous culture equipment supply. John is a regular international speaker on bioprocessing, SME entrepreneurship and business coaching. He is the editor of “Continuous Bioprocessing, Current Practice & Future Potential”, available for free on www.continuous-bioprocessing.com.
Lunch and Networking
Conversion of Adhesion Cell Line to Suspension Perfusion
Matt Zustiak, Manager, Cell Culture Development Group, Patheon Biologics
Abstract
There comes a time during the product life cycle where consideration should be made to updating your legacy process. In this case study we converted an attachment based cell culture production process to a suspension based XCell ATF perfusion process. As a result, we were able to remove animal derived raw materials and significantly increase volumetric productivity while maintaining desired product quality characteristics.
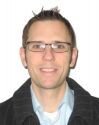
Speaker Bio
Matthew is currently the manager of the Cell culture Development Group at Patheon Biologics in St. Louis, MO. He joined the group in 2013 and has lead the upstream development and characterization of several phase I-III programs for both mAbs and non-mAbs produced in CHO and other cell lines. Prior to Joining Patheon, Matt worked as a Scientist in the Cell Culture Development group for MedImmune. Matt joined MedImmune after completing his graduate work in Chemical and Biomolecular engineering at Johns Hopkins University where he conducted research in engineering CHO cells for enhanced biotherapeutic protein production under the advisement of Prof. Michael Betenbaugh. Matt found his passion for biotherapeutic protein production at the National Cancer Institute where he worked under a contract with Science Applications International Corporation (SAIC) in the Biopharmaceutical Development Program. He Joined SAIC after completing his undergraduate work in Chemical Engineering at the University of Michigan and was fortunate to be a part of a team bringing several early phase molecules expressed in various systems to first in human trials over a period of 10 years.
Accelerating Downstream Process Development Using Small-scale Automated Purification
Brian O'Mara, Senior Scientist, Biologics Process Development Group, Bristol Myers Squibb
Abstract
Traditional downstream process development has relied on standard bench-scale preparative chromatography methods to optimize parameters for clinical and commercial manufacturing. The material demand required for preparative chromatography in combination with low throughput has constrained the advancement of proteins into clinical trials. With the recent advances in miniaturized columns and automated liquid handling, process development time is reduced and an increased body of knowledge is obtained with limited material. Here, we present case studies describing how an automated liquid chromatography system was used in the development of monoclonal antibodies.
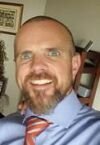
Speaker Bio
Brian is a Senior Scientist in the Downstream Bioprocess Development group at Bristol-Myers Squibb in Seattle, WA. He has been working in the biotech industry since 2000 and previous experience includes Wyeth (Pfizer), University of Rochester, and Genencor International (DuPont). He has worked on a variety of proteins throughout his career for both clinical and commercial development including monoclonal antibodies, vaccines, enzymes, protein conjugates and radiolabeled diagnostics from both microbial and mammalian expression systems. Brian received his BS in Biology from Binghamton University and MS in Chemistry from Lehigh University.
Break
Introducing OPUS® R Columns: Ultimate Flexibility from Pre-packed to Unpacked
Christine Gebski, Vice president, Product Management and Field Applications, Repligen
Abstract
With an innovative side port that allows for simple resin unpacking, OPUS® 45R and OPUS® 60R columns provide the ultimate flexibility in pre-packed column technology. Without compromising chromatographic performance or column cleanability, the new feature helps mitigate the risk of implementing pre-packed columns in cGMP settings, and allows for re-use of the unpacked resin for other purposes. Test results on chromatographic performance, bioburden testing, shipping tests and simple unpacking procedure will be presented.

Speaker Bio
Before joining Repligen in 2015, Christine Gebski was Head of the POROS® Business Unit within the Bioproduction Division of Applied Biosystems/LIFE Technologies/Thermo Fisher Scientific, working with purification products, including POROS® and CaptureSelect® chromatography resins. She managed Global Process Chromatography Applications for ten years, developing collateral and providing technical support, supporting new product development and manufacturing process improvement efforts. She also managed R&D, developing and commercializing three new chromatography resins. Before joining LIFE Technologies, Ms. Gebski was a Process Development Scientist for 15 years in the biotechnology industry, with roles in both development and engineering functions, including developing, scaling, transferring and validating downstream purification processes. She received a B.S. in Biology from the University of Vermont and a M.S. in Biotechnology from the University of Massachusetts at Lowell.
Positive Impact of Pre-packed Columns in a Multi-product Manufacturing Facility
David Briggs, Scientist, Process Sciences, AVID Bioservice
Abstract
Avid BioServices recently commissioned a new commercial facility that exploits single-use and disposable technologies. As part of this plan, Avid implemented the use of Repligen OPUS pre-packed columns in a multi-column process. Their use has led to reduced set-up time, reduced process time, reduced capital and validation expense. This case study will describe the new facility and provide data demonstrating the positive impact of pre-packed columns in a multi-product manufacturing facility.
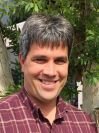
Speaker Bio
David Briggs, Ph.D. is a Scientist in the Process Sciences department at Avid Bioservices. In the Process Sciences department, Dave’s responsibilities include scaling-up and tech transfer of ultrafiltration, viral filtration, and chromatography steps from lab-scale to clinical and commercial scale. Prior to working in Process Sciences, Dave worked as a downstream bioprocessing scientist in MS&T and downstream manufacturing associate in clinical manufacturing. He received his Ph.D. in Molecular Biology & Biochemistry from the University of Arizona.
Panel Discussion and Q&A
Abstract
The speakers will answer your questions in this 15-minute discussion and Q&A session.
Reception and Networking
Discover More Seminars/Technical Roadshows