Seed Train Intensification
Seed train intensification aims to generate ultra high-density cell cultures at optimal points during cell expansion using a robust cell retention device, such as the XCell ATF® Device, prior to the inoculation of the production bioreactor.
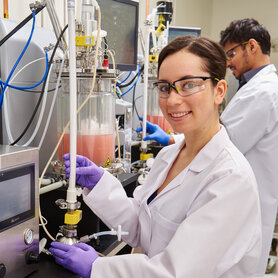
The purpose of a seed train is the generation of an adequate number of cells for the inoculation of a production bioreactor. The cells are usually run through many cultivation systems which become larger with each passage (e.g. T-flasks, roller bottles or shake flasks, small scale bioreactor systems and subsequently larger bioreactors). The production bioreactor (N stage) is inoculated out of the largest seed train scale.
Traditional Seed Train
Challenges
- 3-4 weeks to production bioreactor
- Multiple steps, some require open handling
- Seed variability creates scheduling risk and/or output variability
- 8 steps
- 42 days to product
- 28 days to N
- 14 days in N stage
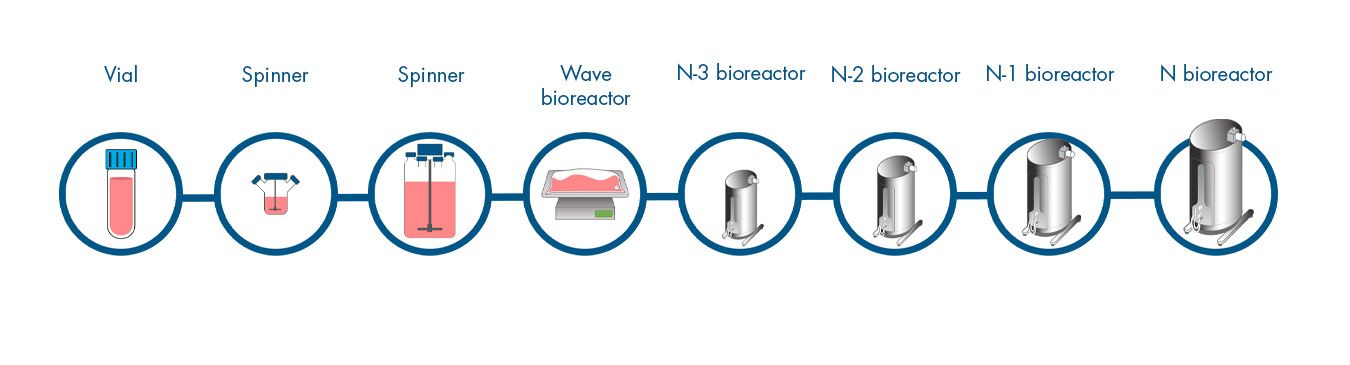
Intensified Seed Train
Intensified seed trains perform process intensification, using a cell retention device such as the XCell ATF® Device, at optimal points during cell expansion to attain the highest cell density inoculum for the production (N) bioreactor. Seed train intensification promotes flexibility and scalability, allowing small labs and global players alike to grow the exact amount of cell culture required, irrespective of whether they are needed for a clinical study, a new therapy or a personalized treatment.
Benefits
- Less time in production reactor
- More batches per year
- Shorter seed train times
- Reduced plant footprint
- Increased flexibility
- Reduced COGs
Repligen solutions help overcome key challenges in seed train intensification, with hands-on process and implementation consultation from global Field Applications Specialists.
OPTION 1 | N-1 Intensification
Intensify cell growth in the step (N-1) prior to the production bioreactor (N). This process intensification is done by attaching a cell retention device to the N-1 bioreactor to attain high cell density and viability. This seeds the production bioreactor at a higher starting cell density and shortens the production bioreactor run time. This can dramatically increase the facility output without direct change to the core production process.
Variations are possible on this theme, depending on existing facility layouts, one common one being that one N-1 bioreactor might inoculate two production vessels.
Click on the workflow link below to find productivity and throughput solutions you can implement today.
- 8 steps
- 37 days to product
- 30 days to N
- 7 days in N stage
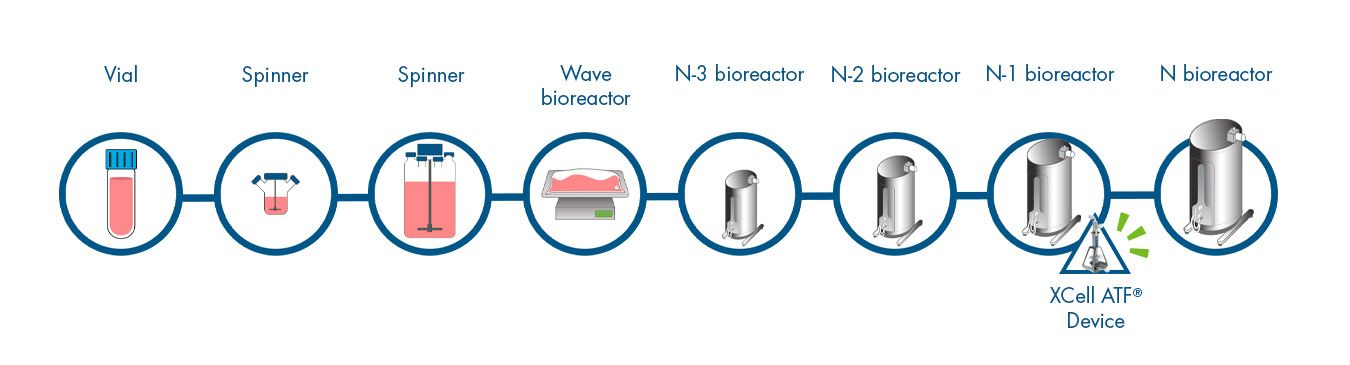
OPTION 2 | N-2 or earlier Intensification
Perform process intensification earlier in the workflow by attaching the XCell ATF® Device to the N-2 or earlier bioreactors. This can save as much as 1 week in the seed train and reduce or eliminate several bioreactors later in the workflow. This means less bioreactors to purchase, operate, clean, and validate - saving clean room floor space while mitigating risk.
Click on the workflow link below to find productivity and throughput solutions you can implement today.
- 6 steps
- 31 days to product
- 24 days to N
- 7 days in N stage
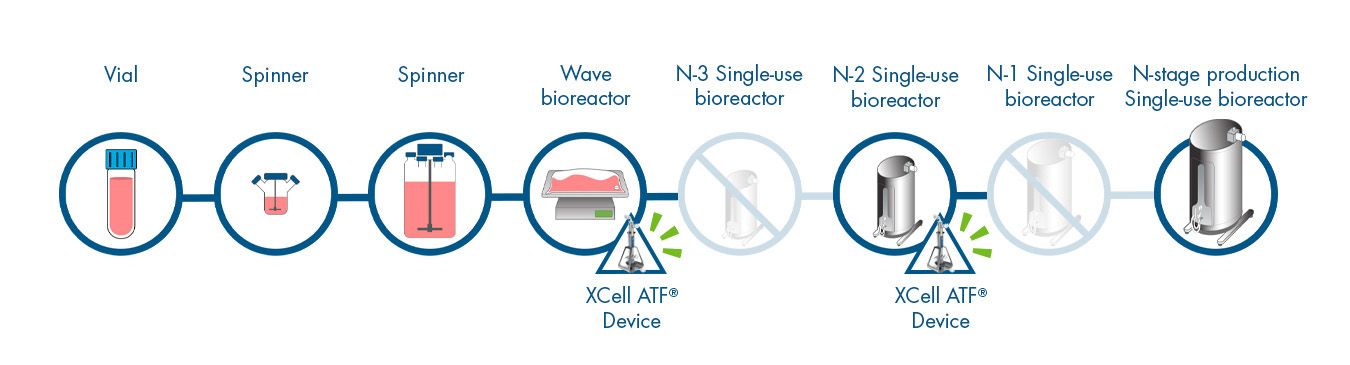
OPTION 3 | Large Volume High Density (LVHD) Frozen Process Intermediaries
De-couple cell bank and variable early cell culture expansion from manufacturing by producing and freezing intermediate cells. This ensures cells of high cell concentration and viability, and known volume, are provided to manufacturing every time. This process intensification option can be performed in a central facility and distributed globally, making scheduling vastly easier with inoculation occurring “on demand”.
Click on the workflow link below to find productivity and throughput solutions you can implement today.
5 steps and time not relevant
(performed outside production timeline)
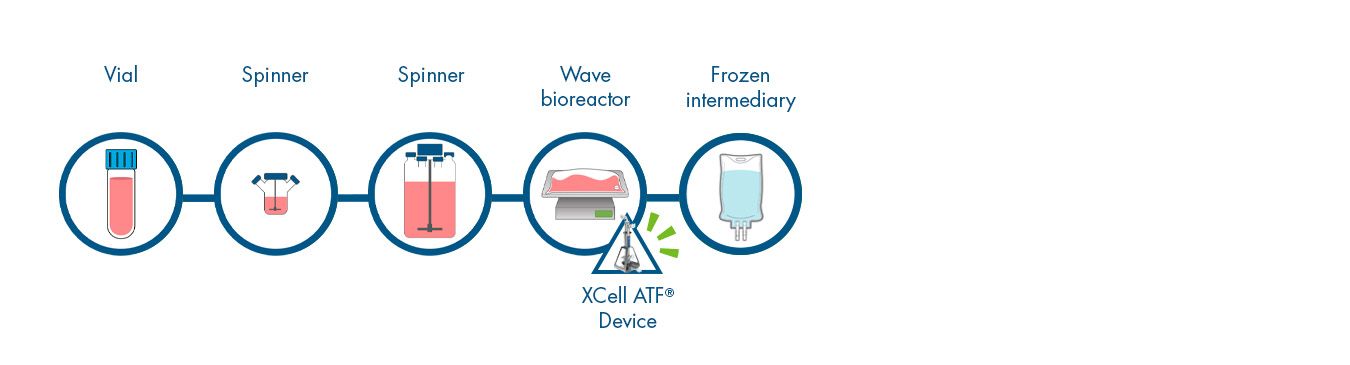
OPTION 4 | Frozen Process Intermediaries with N-1 Intensification
Combine Frozen Process Intermediaries and N-1 or earlier intensification. This enables Manufacturing on Demand, and a truly flexible facility ready for batch or continuous operation.
- Significantly smaller footprint and less equipment
- Reduced CAPEX for equipment and cleanroom
- Fewer operational steps
- More repeatable output
- Faster turnaround of equipment and more batches per year
Click on the workflow link below to find productivity and throughput solutions you can implement today.
- 3 steps
- 13 days to product
- 6 days to N
- 7 days in N stage

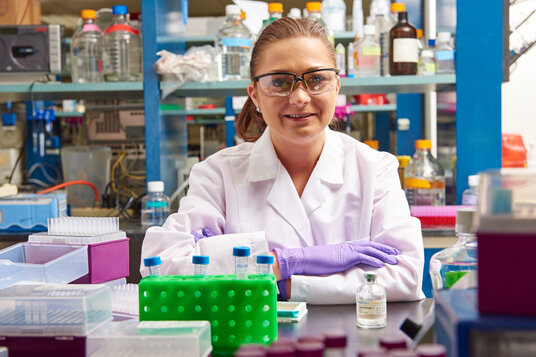
Customer First.
Support is part of the Repligen DNA. Our goal is to provide exceptional customer experience, and to support the efficient and successful adoption and implementation of all Repligen products and services.
- Field Application Support
- Customer Service
- Field Service Engineers